Harnessing the Power of Compression Molding: A Comprehensive Guide to Leading Compression Molding Companies
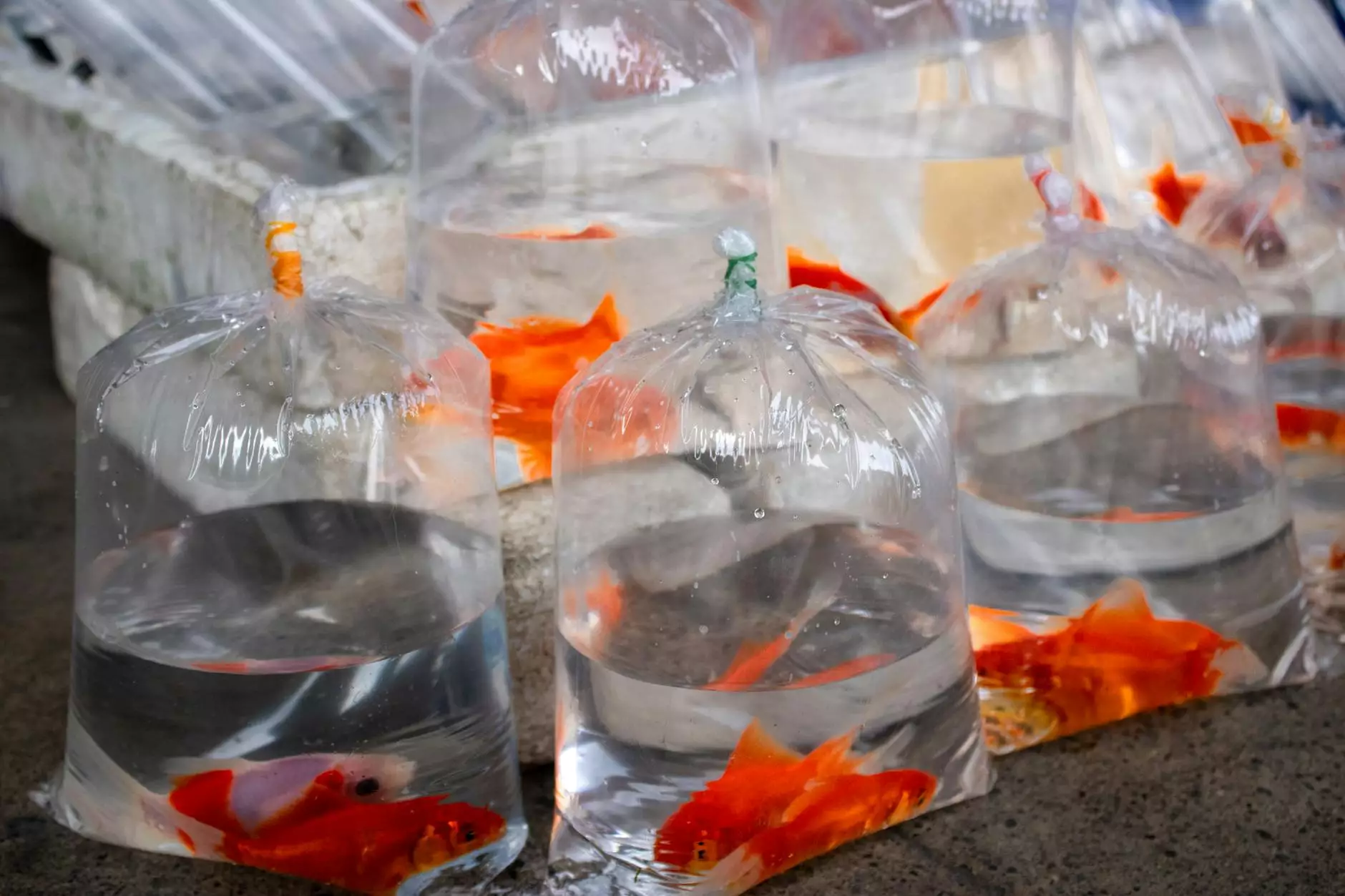
Compression molding companies have revolutionized the manufacturing landscape, delivering innovative solutions that cater to a myriad of industries, including electronics and medical supplies. In this extensive article, we will delve deep into the core functions of these companies, highlighting their importance, the processes they employ, and their significant contributions to various sectors. From ensuring product quality to sparking innovation, the influence of compression molding companies is undeniable.
What is Compression Molding?
Compression molding is a widely used manufacturing process where a polymer is placed into a heated mold cavity. The mold is then closed, and pressure is applied to form the desired shape. This method is particularly beneficial for creating heavy, intricate, and precise components, making it a preferred choice for many compression molding companies.
The Process of Compression Molding
The compression molding process typically follows these steps:
- Material Preparation: The thermosetting or thermoplastic materials are preheated if required, and then cut into specific shapes and sizes.
- Mold Setup: The specially designed mold is prepared, ensuring it is clean and free from residue from previous molding cycles.
- Material Injection: The material is loaded into the mold cavity.
- Heating and Pressurization: The mold is closed and pressure is applied while heat cures the material into its final form.
- Cooling: After sufficient curing, the mold is cooled before the finished part is ejected.
- Finishing Touches: Additional processes, such as trimming and surface finishing, may be applied to enhance the final product.
Why Choose Compression Molding? Benefits for Industries
The advantages of compression molding are manifold, especially for industries such as electronics and medical supplies:
- Cost-Effectiveness: The ability to create large quantities of parts at a lower cost is a significant advantage.
- High Precision: Compression molding ensures that parts are produced with tight tolerances and exact specifications.
- Material Versatility: A wide range of materials can be used, including plastics, rubber, and composite materials.
- Reduced Waste: The process generates minimal waste compared to other molding techniques.
- Complex Designs: It allows for the creation of intricate geometries that can otherwise be challenging to produce.
The Role of Compression Molding Companies in Electronics
The electronics industry continually seeks innovative production methods to support the development of new technologies. Here’s how compression molding companies are essential in this sector:
Product Development and Innovation
The rapid evolution of electronic devices necessitates a fast and flexible manufacturing process. Compression molding allows for quick prototyping and mass production of components such as:
- Enclosures: Molding provides durable enclosures that protect sensitive electronics.
- Connectors: Precision-molded connectors ensure reliable electrical connections in devices.
- Insulators: Custom insulators created via compression molding prevent short circuits and enhance safety.
High-Quality Standards
Quality control in the electronics sector is of utmost importance. Compression molding companies implement strict quality assurance protocols to meet industry standards and regulations. This commitment to quality helps maintain the reliability of electronic products, ultimately benefiting consumers.
The Impact on Medical Supplies
In the medical supplies sector, compression molding companies are instrumental in fabricating components that adhere to stringent safety and effectiveness standards. Here’s an overview of their contributions:
Compliance and Safety
With products like surgical instruments, implants, and medical devices, compliance with health regulations is non-negotiable. Compression molding enables:
- Precise Manufacturing: Parts can be manufactured to exact specifications.
- Biocompatible Materials: Companies can use materials suited for medical applications, ensuring patient safety.
Customization and Scalability
The medical industry often requires unique parts for specific applications. Compression molding allows for rapid customization and scalability:
- Tailored Solutions: Products can be designed to meet specific clinical needs.
- Efficient Scaling: As demand fluctuates, companies can adapt production volumes accordingly without significant downtime.
Choosing the Right Compression Molding Company
When seeking a compression molding company, especially for the electronics or medical supplies industry, consider the following factors:
Experience and Expertise
Look for companies with a proven track record in your industry. Evaluate their portfolio and case studies for insights into their capabilities and innovation.
Quality Assurance Practices
Ensure the company follows strict quality assurance methods that comply with industry standards, such as ISO certifications.
Material Offerings
Consider the range of materials they can work with, as this flexibility often translates to better product performance and application suitability.
Customer Support and Relationships
Building a strong partnership with your supplier is vital. A good compression molding company will offer robust customer service and support throughout the manufacturing process.
Future Trends in Compression Molding
The compression molding industry is continually evolving. Here are a few trends to watch:
Sustainable Manufacturing
As environmental concerns grow, many companies are focusing on sustainable practices. This might include using biodegradable materials or implementing more efficient processes to reduce waste.
Advanced Technologies
Integrating advanced technologies like automation and Industry 4.0 concepts can enhance production efficiency and quality control. Data analytics can provide insights for optimizing production runs.
Customization through 3D Printing
The integration of 3D printing technologies with compression molding processes can pave the way for unprecedented customization and rapid prototyping capabilities.
Conclusion
Compression molding companies play an essential and dynamic role in both the electronics and medical supplies industries. Their ability to deliver high-quality, cost-effective, and customized solutions has earned them a crucial place in today’s manufacturing ecosystem. As these companies continue to innovate and adapt to new technologies and trends, their contributions will undoubtedly shape the future of manufacturing across various sectors.
Get In Touch With Nolato
If you're looking for a reliable partner in your next project, consider reaching out to Nolato. Their expertise in compression molding and dedication to quality make them a leading choice in the industry.
Taking advantage of the incredible benefits of compression molding can help your business enhance product quality, reduce costs, and significantly ramp up production capabilities. The future is bright for businesses that leverage the power of compression molding companies.