Understanding Mold Prototypes in Metal Fabrication
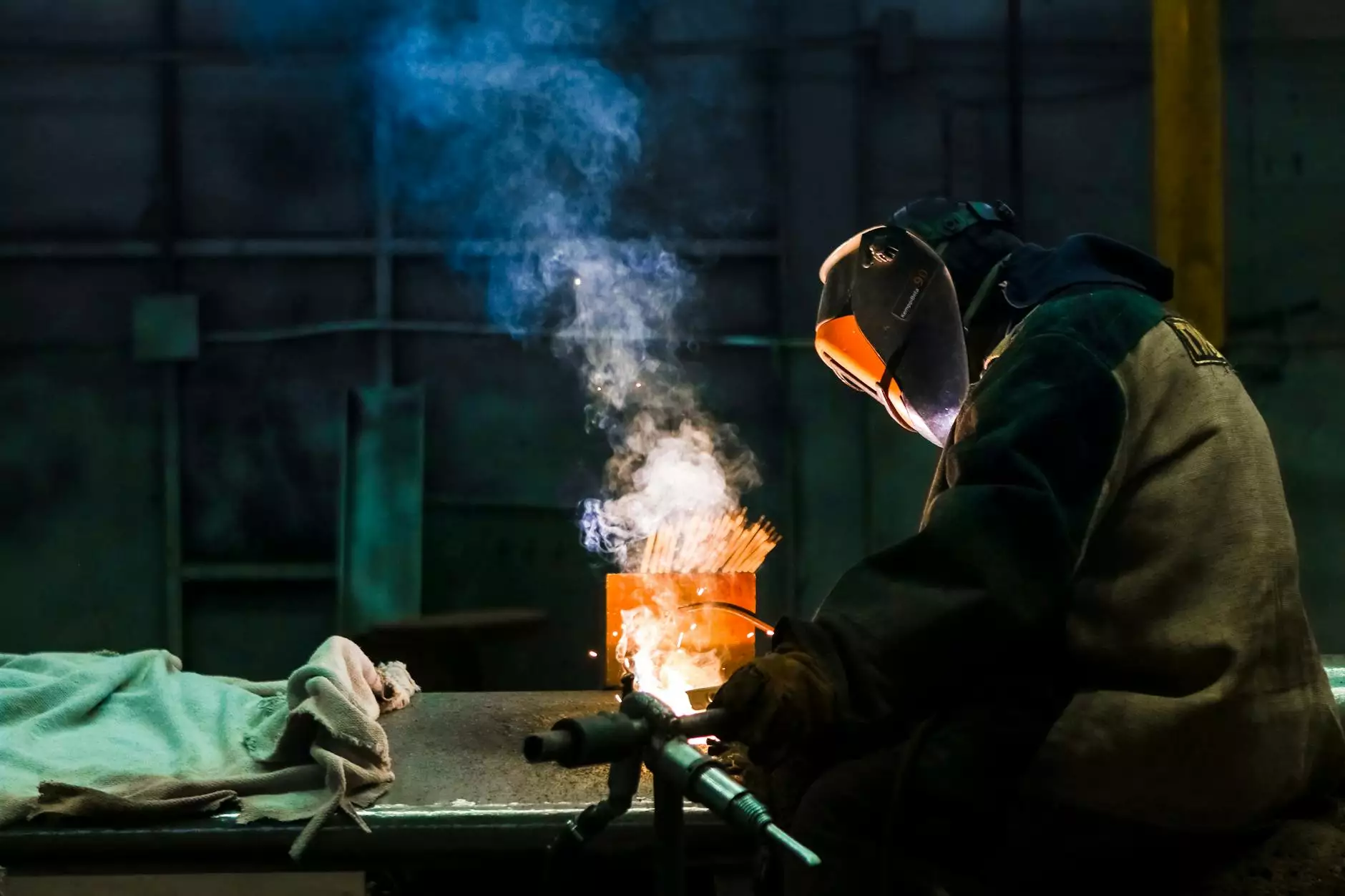
Mold prototypes are an essential part of the product development process, particularly in the realm of metal fabrication. As businesses strive to innovate and create efficient, reliable products, the need for precise molds becomes apparent. This article delves into the intricacies of mold prototypes, their significance, applications, and how they can drive success within a business context.
What is a Mold Prototype?
A mold prototype serves as a preliminary model used in the design and manufacturing process. It allows manufacturers to create a tangible representation of their design before committing to mass production. This is particularly important in metal fabrication, where precision and accuracy are paramount.
The Importance of Mold Prototypes
Mold prototypes play a critical role in various industries, from automotive to aerospace. Understanding their significance can drastically affect a company's efficiency and product quality:
- Cost Savings: Investing in a mold prototype can help identify design flaws early, thus preventing costly mistakes during mass production.
- Enhanced Design Accuracy: Prototypes allow for modifications, ensuring the final product meets the intended specifications.
- Time Efficiency: Rapid prototyping techniques enable quicker iterations and faster turnaround times, keeping projects on schedule.
- Improved Communication: Having a physical model aids in communicating ideas and design concepts among team members and stakeholders.
Types of Mold Prototypes Used in Metal Fabrication
Different types of mold prototypes cater to various stages of product development and production needs. Here’s a closer look at some common types:
1. Functional Prototypes
Functional prototypes are fully operational models used to test design functionality. They provide insights into design performance, usability, and other critical factors.
2. Visual Prototypes
These prototypes focus on the overall aesthetic of the product. They help stakeholders visualize the final product's look and feel, aiding in marketing and design approval processes.
3. Proof-of-Concept Prototypes
These models validate specific ideas or innovations, providing practical demonstrations of technical viability.
The Process of Creating Mold Prototypes
Creating a mold prototype involves several key stages, each requiring careful planning and execution:
1. Concept Development
The first step is to define the concept. This involves gathering input from various stakeholders to create a comprehensive design brief.
2. CAD Modeling
Utilizing Computer-Aided Design (CAD) software, designers create detailed digital models of the mold. This step is critical as it ensures precision and facilitates the design revision process.
3. Prototype Fabrication
Once the CAD model is finalized, the prototype is fabricated using various methods, including:
- CNC Machining: Utilizes computer-controlled machines to cut and shape materials.
- 3D Printing: An increasingly popular technique that builds prototypes layer by layer.
- Injection Molding: Creates high-fidelity prototypes particularly suitable for testing plastic parts.
4. Testing and Evaluation
The fabricated mold prototype undergoes thorough testing to evaluate its performance and adherence to specifications. Any necessary modifications are implemented based on the results.
Benefits of Using Mold Prototypes in Metal Fabrication
The benefits of mold prototypes are extensive and can lead to enhanced product quality and business success:
- Reduction in Production Errors: Early detection of design flaws minimizes the risk of defects in final products.
- Enhanced Collaboration: Physical prototypes facilitate discussions and reviews among teams, fostering a collaborative environment.
- Faster Development Times: Rapid prototyping techniques allow for quicker adjustments, speeding up the overall development cycle.
- Adaptability to Market Feedback: Prototypes enable companies to adapt to consumer feedback, ensuring market-ready products drive sales.
Real-World Applications of Mold Prototypes
Mold prototypes are utilized across various industries. Here are a few noteworthy examples:
1. Automotive Industry
In this industry, mold prototypes are crucial for developing various components, from body parts to engine components. They support the creation of test models that reflect real performance.
2. Aerospace Sector
Given the precision required in aerospace manufacturing, mold prototypes allow engineers to test the aerodynamics and structural integrity of parts, ensuring safety and efficiency.
3. Consumer Electronics
Tech companies rely on mold prototypes to develop ergonomic designs and ensure that the end product meets user expectations in terms of usability and functionality.
Choosing the Right Metal Fabrication Partner for Mold Prototypes
When seeking a reliable partner for mold prototype development, consider the following:
- Experience and Expertise: Ensure the company has significant experience in creating prototypes specifically for metal fabrication.
- Technology and Tools: Check that they utilize advanced technologies like CNC machining and 3D printing for optimal results.
- Quality Control: A robust quality control process should be in place to guarantee the accuracy and reliability of prototypes.
- Customer Service: Strong communication is key. Look for partners who prioritize customer relations and are willing to collaborate closely.
Future Trends in Mold Prototypes
The landscape of mold prototypes is continually evolving. Here are some trends shaping the future:
1. Increased Automation
Automation in machining and production processes enhances efficiency and precision, speeding up prototype creation and reducing costs.
2. Sustainability Focus
With a growing emphasis on sustainability, manufacturers are exploring eco-friendly materials and processes for mold prototypes, aligning with global sustainability goals.
3. Integration of AI and Machine Learning
Artificial intelligence and machine learning are making their way into design processes, offering predictive capabilities and fostering innovation.
Conclusion
In conclusion, mold prototypes are indispensable in the metal fabrication sector. They not only foster innovation and efficiency but also ensure the production of high-quality products that meet market demands. As the industry advances, embracing these prototypes will remain key to maintaining competitive advantages. For businesses looking to excel in design and manufacturing, investing in mold prototypes is not just beneficial; it is essential for future success.