Understanding Tooling Molding and Its Impact on Metal Fabrication
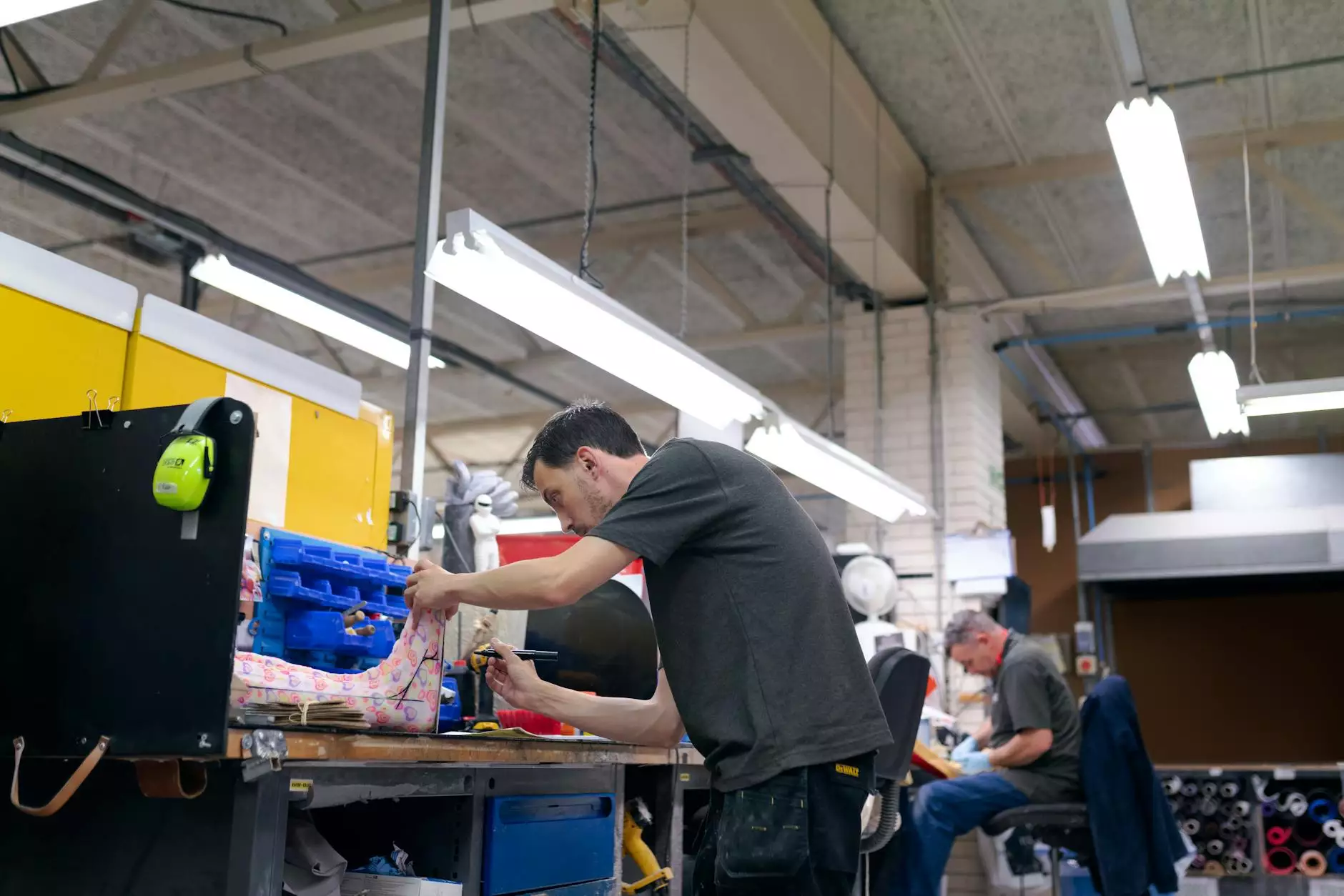
Tooling molding is a pivotal process in the manufacturing sector, particularly within the realm of metal fabrication. This technique not only streamlines production but also enhances the quality of the final products. In this article, we will explore the various dimensions of tooling molding, its applications, and its significance for businesses, particularly in the metal fabrication industry.
What is Tooling Molding?
At its core, tooling molding refers to the creation of precise molds that shape molten materials into desired forms. This process is essential for producing parts with intricate designs and high tolerances. The tooling involves various materials, such as steel, aluminum, and polymer, depending on the characteristics required in the final product.
The Process of Tooling Molding
The process of tooling molding can be broken down into several key stages:
- Designing the Mold: Initially, engineers use computer-aided design (CAD) software to create a detailed mold design. This step is critical as it determines the accuracy and functionality of the mold.
- Fabricating the Mold: Once the design is approved, the fabrication of the mold begins. This may involve CNC machining, electrical discharge machining (EDM), and other advanced manufacturing techniques.
- Testing the Mold: Before mass production, the mold undergoes rigorous testing to ensure it meets the necessary specifications. Adjustments are made as needed to ensure accuracy and quality.
- Production: After successful testing, the mold is ready for production. Materials are heated and poured into the mold, taking on the desired shape as they cool.
- Finishing: Lastly, any finishing processes, such as polishing or coating, are applied to ensure the final product meets quality standards.
Applications of Tooling Molding in Metal Fabrication
Tooling molding finds extensive applications in various sectors of metal fabrication. Here are some areas where its impact is particularly pronounced:
1. Automotive Industry
The automotive industry relies heavily on tooling molding for producing components such as engine parts, frame structures, and intricate interior elements. The precision offered through this process contributes to enhanced vehicle performance and safety.
2. Aerospace Sector
In the aerospace industry, the tolerance and weight specifications are extremely strict. Tooling molding allows manufacturers to create lightweight yet strong components that adhere to these rigorous standards.
3. Consumer Electronics
From smartphone casings to internal components, tooling molding is crucial in ensuring that consumer electronics are not only functional but also aesthetically pleasing. The intricate designs made possible by this process meet the demands of modern consumers.
Benefits of Tooling Molding for Businesses
Investing in tooling molding technologies can offer a multitude of benefits for businesses involved in metal fabrication:
- Increased Efficiency: Tooling molding significantly reduces production time, allowing companies to meet deadlines and increase output.
- Cost-effectiveness: Although the initial investment in molds can be high, the overall cost per part decreases with mass production, leading to higher profit margins.
- Quality Assurance: Consistency in quality is a hallmark of tooling molding. The precise nature of molds ensures that each part produced meets the same high standards.
- Design Flexibility: Tooling molding allows for a variety of designs, accommodating complex shapes that would be difficult, if not impossible, to achieve through traditional manufacturing methods.
The Future of Tooling Molding in Metal Fabrication
Looking ahead, the future of tooling molding in metal fabrication seems promising, driven by several trends:
1. Advances in Technology
Technological advancements, including 3D printing and automation, are set to revolutionize tooling molding. These innovations will enhance precision, reduce lead times, and lower costs.
2. Sustainability Focus
As industries shift towards sustainable practices, tooling molding offers opportunities for reduced waste and energy consumption. Eco-friendly materials and processes are becoming more prevalent.
3. Customization
The demand for customized products is on the rise. Tooling molding provides the flexibility needed for bespoke designs, catering to specific customer needs without significant increases in costs.
Conclusion
In conclusion, tooling molding is a cornerstone of the metal fabrication process, offering numerous advantages that drive efficiency and quality. As businesses like Deep Mould continue to adopt advanced tooling techniques, they position themselves to thrive in a competitive marketplace. Embracing these innovations will not only enhance operational capabilities but also open new avenues for growth and customer satisfaction.
By understanding and leveraging the capabilities of tooling molding, businesses can stay ahead in an ever-evolving industry landscape, ensuring they meet the demands of the future.