The Art and Innovation of Vacuum Casting
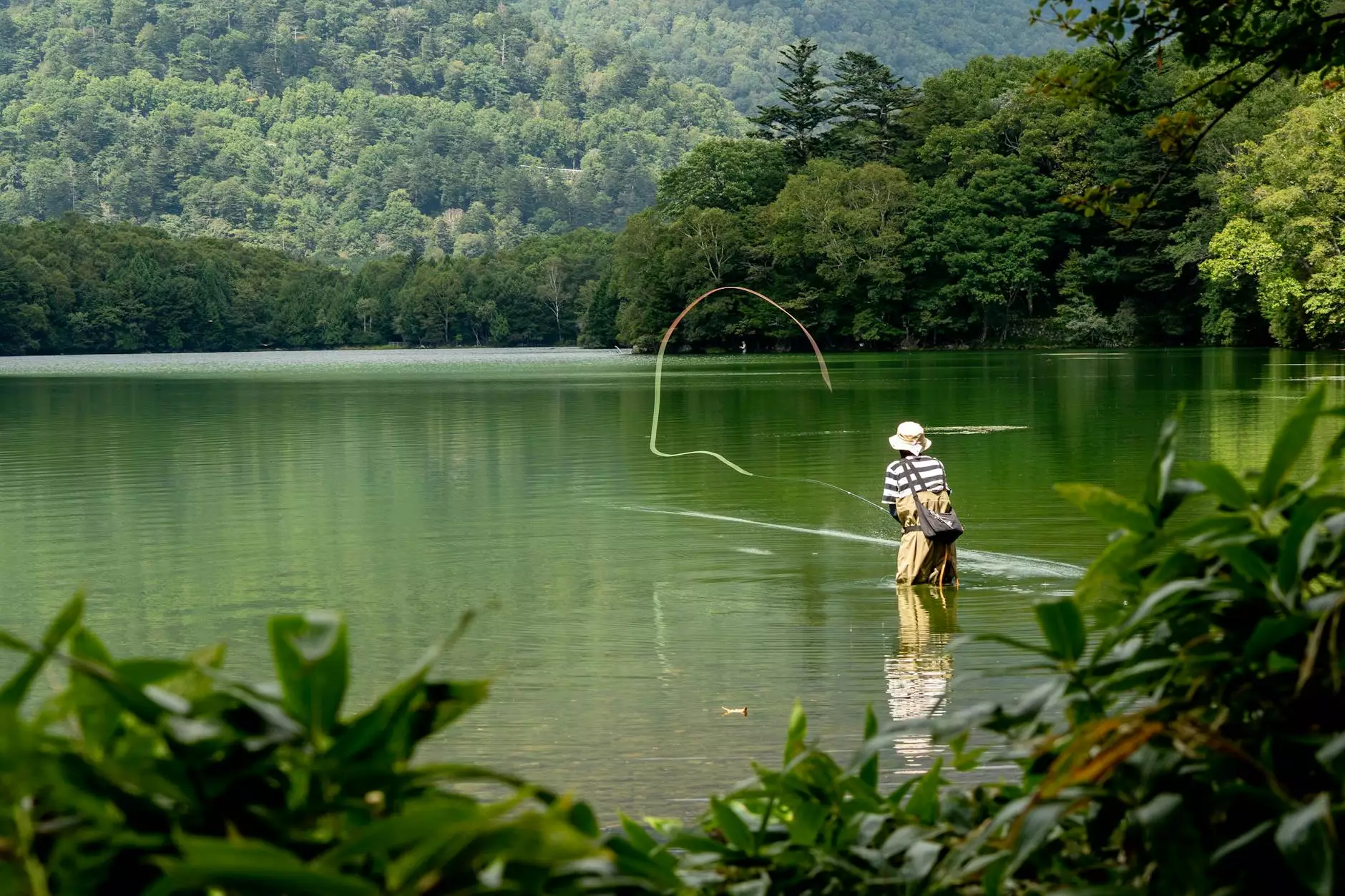
Vacuum casting is a revolutionary technique that has transformed the landscape of manufacturing, product design, and 3D printing. It plays a pivotal role in creating high-quality prototypes and limited-run production components. In this detailed article, we will delve deep into the nuances of vacuum casting, discussing its benefits, techniques, and applications across various industries.
What is Vacuum Casting?
Vacuum casting is a process that involves creating a mold using a master model, typically produced through 3D printing or other methods. This mold is then filled with polyurethane or silicone materials, which cures under vacuum pressure. This ensures the elimination of air bubbles, leading to smooth and precise replicas of the desired object.
Unlike traditional manufacturing methods, vacuum casting allows for rapid production and is particularly advantageous for companies looking to test products or produce small batches efficiently.
The Process of Vacuum Casting
The vacuum casting process can be broken down into several key steps:
- Creating the Master Model: The first step involves producing a master model, often using 3D printing technology for precision.
- Making the Mold: A silicone mold is created around the master. This is done by pouring silicone rubber over the master model.
- Preparing the Casting Material: After the mold cures, it is prepared for casting. Polyurethane or other casting materials are chosen based on the final product requirements.
- Vacuum Filling: The mold is placed inside a vacuum chamber, and the chosen material is poured in. The vacuum removes air, helping the material flow into all parts of the mold.
- Curing: The casting material is then allowed to cure, typically within a few hours.
- Finishing Touches: Once cured, the mold is demolded, and any necessary finishing work is completed.
Benefits of Vacuum Casting
Vacuum casting offers numerous advantages, making it a popular choice for manufacturers and designers alike:
- High Precision and Detail: The vacuum process ensures that even the most intricate designs are replicated with remarkable accuracy.
- Quick Turnaround Times: With the ability to produce molds and castings in a short time, businesses can reduce their time-to-market significantly.
- Cost-Effective for Small Runs: Unlike traditional mass production, vacuum casting is especially economical for small production runs, allowing companies to save on costs.
- Diverse Material Options: Various materials can be used in vacuum casting, including flexible and rigid plastics that resemble different finishes and textures.
- Customization: Businesses can easily adapt their prototypes and products for different markets through minor adjustments in the mold-making process.
Applications of Vacuum Casting
Vacuum casting is widely used across different sectors, including:
1. Product Design and Development
In the realm of product design, rapid prototyping is key. Companies like arti90.com utilize vacuum casting to create realistic prototypes quickly, allowing designers to test functionality, ergonomics, and appeal before production. This minimizes risks and aligns the products more closely with consumer expectations.
2. Art Supplies and Sculpting
Artists and sculptors leverage vacuum casting to replicate intricate designs in art supplies. This method enables the creation of limited edition sculptures or art pieces that retain the original details, thereby increasing the artwork's value and accessibility.
3. 3D Printing and Manufacturing
When combined with 3D printing, vacuum casting enhances the manufacturing process. The ability to create a master model through 3D printing and then use vacuum casting for production blends the best of both worlds—speed and precision in manufacturing.
Materials Used in Vacuum Casting
The choice of material in vacuum casting is critical and can significantly influence the final product’s characteristics. Common materials include:
- Polyurethane: This is the most widely used material due to its versatility and ability to mimic various finishes, from rubbery to hard plastic.
- Silicone: Often chosen for flexible casting applications, providing a soft touch and flexibility.
- Resin: Applicable in cases requiring robust and durable solutions, offering excellent strength and finish.
Tips for Successful Vacuum Casting
To achieve the best results in vacuum casting, consider the following tips:
- Invest in Quality Molds: High-quality silicone molds ensure durability and repeatability in casting.
- Temperature Control: Maintain appropriate temperatures during curing to avoid imperfections.
- Thorough Mixing: Ensure that the casting material is mixed thoroughly to achieve consistent results.
- Proper Ventilation: Make sure to design vent holes in your molds to prevent air traps, enhancing the final product quality.
The Future of Vacuum Casting
The future of vacuum casting looks promising with advancements in technologies. Innovations in materials and techniques are expected to improve the quality and efficiency of the casting process. Integration with automated systems and AI-driven design tools is also anticipated to streamline workflows, reduce labor costs, and elevate accuracy. As industries continue to demand quicker and more cost-effective prototyping solutions, vacuum casting will undoubtedly remain an essential technique in the manufacturing landscape.
Conclusion
In conclusion, vacuum casting is an indispensable method in the fields of product design, art supplies, and 3D printing. Its ability to produce high-quality, precise prototypes quickly and cost-effectively makes it a preferred choice among manufacturers and designers alike. As we advance into an era of rapid technological innovation, vacuum casting will continue to evolve and shape the future of various industries, enabling businesses to turn their creative visions into reality efficiently.
Explore More at Arti90.com
If you're looking for information on art supplies, product design, or enhancing your business capabilities with vacuum casting, do visit arti90.com for more insights and resources.